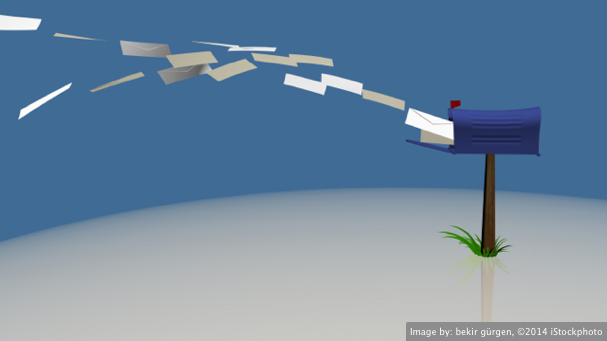
I’ve talked at length about automation and a bullet-proof process in recent posts. It may seem futuristic, but it’s closer than you think, or want it to be, if you’re not prepared. Considering upcoming changes with respect to Full-Service and Seamless Acceptance, the future is right around the corner. The point of my previous posts has been to reduce as much risk and human error as possible. Technology exists to do just that by addressing the connective processes between manufacturing steps. What about pressing concerns right now though?
Two major concerns I’ve heard from mailers are what to do with undocumented mail trays and extra trays created when mail piece thickness exceeds the estimate. There are solutions to accommodate this with post-processing software, but there are still "holes" in the process when it comes to the digital and physical worlds connecting. Digital solutions are good, but the physical or manual processes are not truly connected to them, and this leads to errors or "holes” in the audit trail and, consequently, risk. With increasing standards on your mailer "report card" from the United States Postal Service (USPS), these are real concerns. The challenge is to handle these trays in a more streamlined process during manufacturing without creating undue rework of trays. How can we catch those exceptions and handle them as part of normal, traceable manufacturing?
The trouble with processing files and creating the subsequent digital document for payment, tray tags, pallet placards, etc. is that without tracking the actual produced mail/trays/paperwork and comparing it to the digital trail in real time, it creates a manually intensive and subject-to-error process. The dreaded job ticket, quality control paperwork, job closeout, reconcile or whatever process you use may work but is typically time-consuming and fraught with potential for errors. There has to be a better way, and with the changes coming, we have to build a better mousetrap.
Consider the following process as a high-level solution: Files are processed and sent to the production floor for manufacturing WITHOUT tray tags, pallet placards or final statements. There is a simple job ticket with initial tray/piece counts and samples. As trays are filled with finished mail, the first and last piece in each tray is bounced off the manifest to generate the appropriate tray tag at the inserter cell. (This actually happens now but in the print room, instead of at the inserter, just in time.) Now, you have the right tag, on the right tray, one at a time, instead of ALL the tags sitting on a work surface in an already tight inserter work cell.
Next, if the piece count is wrong and an additional tag is needed, a sister tag is generated and placed on the tray. Finished trays are placed onto a takeaway conveyor that merges all trays into a single takeaway line. Scan points in the conveyor validate and divert rejected trays that don’t match the manifest or a duplicate tag (within the job, or last 45 days) MID, CRID or CIN codes, etc. Trays travel to the finishing area to be sleeved and strapped in-line, diverted to the appropriate pallet separation, where placards are generated and pallets wrapped. Multiple scans are performed to ensure the right trays go to the right pallet and are co-palletized. Tray counts, weights, pallet placards, etc. are digitally adjusted in the final statement submission and exception trays are fixed and re-introduced onto the takeaway line for normal processing.
Think it’s not already happening, or you can’t afford the investment in change? It’s already happening at leading producers. Re-engineering a manual process to a more automated one, reducing risk and improving bottom line performance should be an ongoing goal. Full-Service and Seamless Acceptance is simply more and better reasons to do so, since the ante just keeps going up.
Two major concerns I’ve heard from mailers are what to do with undocumented mail trays and extra trays created when mail piece thickness exceeds the estimate. There are solutions to accommodate this with post-processing software, but there are still "holes" in the process when it comes to the digital and physical worlds connecting. Digital solutions are good, but the physical or manual processes are not truly connected to them, and this leads to errors or "holes” in the audit trail and, consequently, risk. With increasing standards on your mailer "report card" from the United States Postal Service (USPS), these are real concerns. The challenge is to handle these trays in a more streamlined process during manufacturing without creating undue rework of trays. How can we catch those exceptions and handle them as part of normal, traceable manufacturing?
The trouble with processing files and creating the subsequent digital document for payment, tray tags, pallet placards, etc. is that without tracking the actual produced mail/trays/paperwork and comparing it to the digital trail in real time, it creates a manually intensive and subject-to-error process. The dreaded job ticket, quality control paperwork, job closeout, reconcile or whatever process you use may work but is typically time-consuming and fraught with potential for errors. There has to be a better way, and with the changes coming, we have to build a better mousetrap.
Re-engineering a manual process to a more automated one, reducing risk and improving bottom line performance should be an ongoing goal.
Consider the following process as a high-level solution: Files are processed and sent to the production floor for manufacturing WITHOUT tray tags, pallet placards or final statements. There is a simple job ticket with initial tray/piece counts and samples. As trays are filled with finished mail, the first and last piece in each tray is bounced off the manifest to generate the appropriate tray tag at the inserter cell. (This actually happens now but in the print room, instead of at the inserter, just in time.) Now, you have the right tag, on the right tray, one at a time, instead of ALL the tags sitting on a work surface in an already tight inserter work cell.
Next, if the piece count is wrong and an additional tag is needed, a sister tag is generated and placed on the tray. Finished trays are placed onto a takeaway conveyor that merges all trays into a single takeaway line. Scan points in the conveyor validate and divert rejected trays that don’t match the manifest or a duplicate tag (within the job, or last 45 days) MID, CRID or CIN codes, etc. Trays travel to the finishing area to be sleeved and strapped in-line, diverted to the appropriate pallet separation, where placards are generated and pallets wrapped. Multiple scans are performed to ensure the right trays go to the right pallet and are co-palletized. Tray counts, weights, pallet placards, etc. are digitally adjusted in the final statement submission and exception trays are fixed and re-introduced onto the takeaway line for normal processing.
Think it’s not already happening, or you can’t afford the investment in change? It’s already happening at leading producers. Re-engineering a manual process to a more automated one, reducing risk and improving bottom line performance should be an ongoing goal. Full-Service and Seamless Acceptance is simply more and better reasons to do so, since the ante just keeps going up.
Fritz Buglewicz has 20+ years of experience with project management, procedural analysis and business development in print to mail and document management operations. Contact him at fritzb@captechno.com.